Quality
Managing the quality of the products manufactured by Servier is an essential part of providing the best service possible to the patient that uses our products. Our main objectives are to:
- Ensure that our products are manufactured and distributed according to international regulations and the registered specifications
- Manage the quality of suppliers of raw materials and packaging materials
- Successfully pass inspections conducted by health authorities, as well as customer audits
- Ensure the consistency of key quality practices within the global industrial Servier network
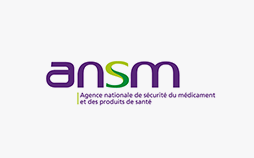
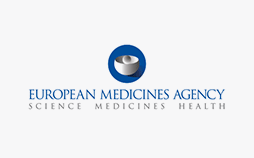
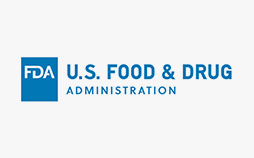
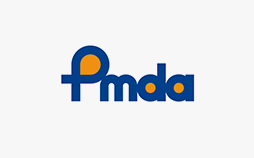
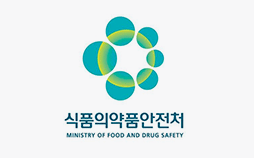
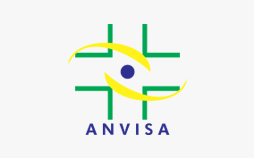
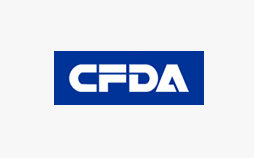
Patient safety is the most important goal for any pharmaceutical manufacturer. The quality of a drug substance or product is directly linked to the manufacturing process and quality control at every site. Management must ensure that process variation is eliminated, consistent quality is guaranteed, and there are no implications for patient safety or security of supply. To assure quality, Servier takes a holistic approach, bringing people, process and policy together to create an efficient, agile quality assurance/quality control (QA/QC) culture.
The success of every company developing and producing finished drug product, active pharmaceutical ingredients, excipients or raw materials is dependent on an institutionalized quality effort. Quality assurance/quality control is an essential element of Servier’s commitment to operational excellence across our contract development and manufacturing operations.
Quality Risk Management
Strong process design and control strategies at the production line level are an important element of our quality management. Also, our robust quality regime and the institutional framework to support an effective quality management system (QMS), quality risk management (QRM) approaches, and a continuous improvement program are critical to managing risk and sustaining product quality.
A sustainable, high-performing quality regime seeks transparency and collaboration from all facets of the organization, spanning operations, procurement and executive management. Our focus on quality also requires an interdisciplinary approach that promotes collaboration and institutional culture. Local teams are managed through a core corporate QMS team that ensures consistency of QA/QC activities across Servier’s global manufacturing operations.
Quality Systems Review
Servier quality relies on a proactive quality system review (QSR) process based on audits, process data analysis, equipment condition, and periodic review of internal and external sources of data or inputs for QRM. The goal of identifying and listing risks is to assign priority and address it commensurate to its relative threat, the highest threat being anything that would potentially impact patient safety. An internal strategy is then defined with the appropriate tools to manage CAPA response efficiently. Servier quality personnel, for example, are trained extensively to identify operational risk, and are provided with the means to collect the best data before ultimately implementing the corrective process to fix the problem.
More than Passing Inspection
Proactive compliance at Servier manifests itself as a “Right First Time” ethic. Being proactively compliant means not waiting for an issue to arise, but to anticipate it, thinking ahead so that the organization can respond more efficiently with a high-performing response. Compliance strategy based on remediation can be shortsighted and become a drag on operations. To combat this, Servier’s corporate QMS monitors anticipate regulatory change in order to craft the best policies and the most cost-effective solutions. To emerge ahead of compliance, Servier’s quality team assesses regulatory guidance as it arises to determine the impact on operating units, especially in regions that the QMS team understands will be expecting new or revised guidelines in the near future.
Approximately 10 years ago, Servier instituted a comprehensive intersite corporate audit program that brings the company’s quality managers to perform audits together annually. During this time, the team reviews the performance of each of the eleven sites, with the end goal being to increase the harmonization of the total organization. Servier conducts its own audits of select facilities and then invites quality managers from those facilities to present their findings to colleagues. This effort has proven to be very effective in aligning corporate and local QMS. Indeed, Servier’s annual audit program is key in developing continuity. These efforts cascade across the enterprise via best practice sharing and the promotion of QMS efficiency.